Updated April, 2025
Just 48 % of enterprise digital initiatives meet or exceed their business-outcome targets–leaving more than half stalled in execution limbo. At the same time, 95 % of automation decision-makers now call process automation “critical” to corporate strategy. Those two numbers tell the same story from opposite sides: executives know automation matters, yet most transformation programs still underdeliver.
For CTOs, programme managers, and P&L owners, the cost of that gap is concrete:
- Lost velocity. Product backlogs pile up as hand-offs bounce between siloed teams.
- Hidden labour waste. Manual reconciliations swallow hours that should fund innovation.
- Eroded trust. Sponsors see “digital” as slide-ware rather than an operational muscle.
Digital Process Automation (DPA) fixes the mechanics, not just the messaging. By orchestrating people, data, and systems around rule-based workflows, DPA translates board-level intent into routines that frontline teams can run every day. Market analysts already track a $13 B market growing at 13 % CAGR for DPA platforms-proof that the tooling is ready.
What you’ll get from this guide
- A clear definition of DPA-and how it differs from RPA or generic “automation.”
- A five-step implementation roadmap anchored in DevPulse’s client playbooks.
- KPI frameworks and governance tips to keep momentum once pilots ship.
- Practical work-arounds for integration debt, change resistance, and compliance drag.
Throughout, we’ll link to deeper DevPulse resources-our Agile Transformation Roadmap and Legacy Modernization Guide-so you can zoom into adjacent challenges without losing the strategic thread.
Next up: What Digital Process Automation Really Is (and Isn’t)-including the business cases we see most often in manufacturing, finance, and healthcare.
What Is Digital Process Automation (DPA)?
Digital Process Automation (DPA) is the discipline of redesigning and orchestrating end-to-end business workflows-data, people, and legacy apps included-through a low-code platform that enforces rules, escalations, and real-time monitoring. Where classic Business Process Automation (BPA) focused on single systems (e.g., an ERP approval loop), and Robotic Process Automation (RPA) scripts automate narrow, UI-level tasks, DPA spans the entire value stream-from first customer touch to final reconciliation-so strategy survives the journey to execution.
Automation layer | Scope | Typical ROI window | Best for… |
RPA | Single, repetitive tasks (copy-paste, data entry) | Weeks | Quick cost take-out when APIs are missing |
BPA | Function-specific processes inside one system | Months | Departmental efficiency (e.g., AP invoice matching) |
DPA | Cross-system, cross-team workflows tied to KPIs | Quarters | Strategy execution at enterprise scale |
Why it matters to enterprise leaders
- Strategic leverage. Because DPA embeds business rules directly into workflows, policy changes propagate instantly-no slide decks required.
- Customer experience. DPA removes swivel-chair delays between sales, finance, and ops, shrinking cycle times and error rates simultaneously.
- Platform momentum. Analyst data shows the combined low-code + DPA market hit $13.2 billion by end-2023 and is still compounding ~20 % YoY. Executives are voting with budgets.
Where DevPulse fits
Our modernization practice treats DPA as the connective tissue between two recurring projects:
- Legacy System Modernization → once the monolith is service-enabled, DPA threads those new APIs into streamlined workflows.
- Agile Transformation → teams adopt shorter feedback loops; DPA ensures hand-offs and approvals move just as fast.
Internal follow-ups
– See our Legacy Modernization Guide for API-first refactoring tactics.
– Compare governance metrics in the Agile Transformation Roadmap to the KPI model we’ll outline later in this article.
Why Execution Breaks Down in Large Enterprises
Even the best-crafted digital strategy can stall once it collides with day-to-day realities inside a complex organisation. Three patterns surface in nearly every DevPulse engagement:
Friction Point | Evidence & Impact | Why It Persists |
Functional silos block end-to-end flow | – 82 % of enterprises say siloed data disrupts critical workflows IBM – United States– Approvals ricochet across email threads; cycle times stretch from hours to days | Organisational charts reward department outcomes, not cross-stream KPIs |
Manual “glue work” drains capacity | – 73 % of companies still burn time on manual data entry and validation Vena– Talent that should drive innovation reconciles spreadsheets instead | Legacy systems lack APIs; quick fixes (spreadsheets, email) become permanent |
Legacy architectures resist change | – Batch jobs, on-prem queues, and hard-coded business rules lock strategy to release calendars | Modernisation is tackled piecemeal, leaving execution gaps between new and old stacks |
Executives try to compensate with more meetings or project dashboards, but the root cause is mechanical: the process itself can’t move as quickly as the strategy evolves.
Spot the Symptoms Early
- Mismatch between OKRs and team backlogs. If a quarter ends with roadmap items 40 % complete while revenue goals are on track, you’re tracking outputs, not outcomes.
- Shadow IT workarounds. When marketing exports CRM data to Excel for weekly reports, automation debt is already accruing.
- “Zombie” transformation projects. Initiatives keep their funding but deliver no measurable KPI lift-often a hint that workflows span too many brittle integrations.
Related Deep-Dives
- How silo-busting accelerates digital transformation programmes
- API patterns for legacy system modernization
- Aligning workflows with agile cadences in the Agile Transformation Roadmap
Service tie-in: If these pain points ring familiar, explore our Digital Transformation Solutions or schedule a technical assessment via Tech Consulting Services-we’ll map the process debt hidden between your strategy decks and production systems.
How Digital Process Automation Closes the Gap-Five-Step Roadmap
Time-boxed pilots beat “big-bang” rewrites. Each step below is designed to deliver a measurable win inside one quarter, then compound momentum across the portfolio.
# | Step | What to Do | Key Outputs |
1 | Map & Prioritise the Value Stream | Run a two-day workshop to visualise every hop from customer request to cash-book entry. Sort candidates by cycle-time pain and FTE hours wasted. | – Ranked backlog of automation opportunities- Executive sponsor named for the top workflow |
2 | Build a Low-Code Pilot | Configure the highest-value flow in a DPA platform (e.g., Appian, Pega, Camunda). Keep scope ≤ 10 user stories so payback is obvious. Forrester TEI studies report ROI up to 253 % with seven-month payback for low-code DPA pilots. LLCBuddy | – Deployed pilot with live KPIs- Playbook for additional flows |
3 | Harden the Integration Layer | Expose legacy rules via REST or event queues, then wrap security, logging, and exception handling. This is where DevPulse’s Legacy System Modernization Guide and Modern Tech-Stack Guide shorten the re-platform effort. | – API endpoints / queues in production- Audit-ready governance model |
4 | Scale with Fusion Teams | Form pods of process owners, citizen developers, and platform engineers. Nearly 79 % of organisations now co-develop with low-code “fusion” teams-a model that slashes delivery time by 50-90 %. FlowForma See DevPulse’s Agile Transformation Roadmap for sprint cadences that fit. | – Playbook replicated across 2-3 new flows per sprint- Internal Center of Excellence chartered |
5 | Instrument, Learn, Optimise | Track cycle time, touchless-order % and FTE hours saved in a real-time dashboard. Review deltas at each sprint retro; queue refinements or new automations. Link dashboards to exec OKRs so sponsors see lift monthly. | – Live KPI dashboard- Quarterly ROI report- Continuous-improvement backlog |
Implementation Tips
- Anchor every user story to a business OKR. If it doesn’t tie to revenue, cost, or risk, park it.
- Automate governance as code. Embed SOC-2 controls and exception paths inside the DPA flow-no extra audit checklist required.
Package metrics in a “Friday Flash” email. A one-page snapshot of hours saved and cycle-time delta keeps leadership attention high.
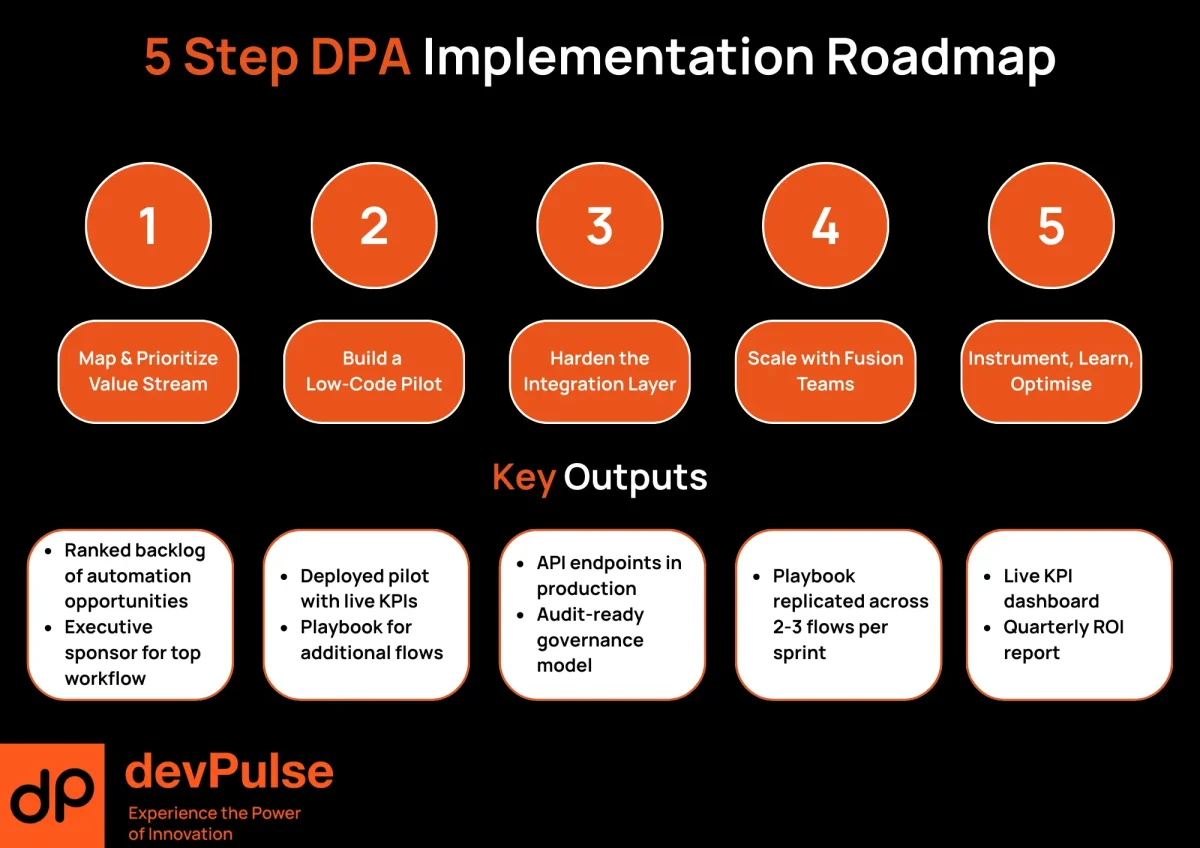
Measuring Success & Driving Continuous Improvement
A DPA program succeeds only if the numbers prove it. Before the first user story reaches staging, engineering and finance should agree on one scoreboard that everyone-from product owners to CFO-can read at a glance.
1 – Pick KPIs That Expose the Whole Flow
Focus on indicators that cross departmental lines; silo-level metrics mask the very frictions DPA is meant to remove.
Metric | Why It Matters | Baseline Target* |
End-to-end cycle time (request → cash) | Captures delays hidden between systems or teams | -30 – 50 % within 2 quarters |
Touchless-order rate | Shows how many transactions complete with zero human intervention | ≥70 % for mature flows Supply & Demand Chain Executive |
First-pass yield / error rate | Quality proxy; each rework loop kills margin | ≤2 % error after stabilisation |
FTE hours returned | Converts efficiency into budget and capacity | 1-2 FTEs per automated flow typical, per SAPinsider 2024 study |
*Targets reflect median improvements cited in recent Everest Group and SAPinsider research; adjust for process complexity and regulatory constraints.
2 – Instrument Early, Audit Often
- Embed telemetry in the workflow model itself. Most low-code DPA suites log step duration and exception paths by default-pipe that data straight to your BI layer rather than exporting CSVs later.
- Link dashboards to executive OKRs. When “Order-to-Cash < 24 hours” is visible on the same screen as revenue targets, sponsorship never wavers.
- Run monthly “KPI retro” sessions. Treat metrics like code: inspect, hypothesise, iterate. Small tweaks-re-sequencing approvals, shortening reconciliation batches-often deliver the steepest slope on the ROI curve.
3 – Close the Loop With Cost & Growth Signals
Financial controllers care about payback, not process minutiae. Translate operational wins into cashable outcomes:
- Cost-to-serve: Multiply FTE hours returned by loaded hourly rates; validate against finance ledger.
- Revenue lift: Faster cycle time brings forward billable milestones-track cash-flow acceleration explicitly.
- Risk exposure: Fewer manual touches mean fewer SOX or GDPR exceptions; quantify avoided fines or audit findings.
Tip: DevPulse’s data team routinely layers DPA logs over revenue and compliance datasets using the event schema described in our Modern Tech-Stack Guide-worth a read if your BI plumbing is still report-heavy.
4 – Publish Wins, Reinvest the Budget
Once the first flow hits its targets, publicise the result company-wide-screenshots of the dashboard, before-and-after numbers, and a short quote from the process owner. The same presentation becomes the business case for the next automation sprint and, ultimately, your Center of Excellence charter.
Common Challenges-and Practical Fixes
1 – Leadership Buy-In Wavers Mid-Project
Only 38 % of executives say they have senior-leadership support for new tech roll-outs-a sharp rise from 10 % two years ago but still far from universal. Backlinko
Fix: lock sponsorship to a hard metric (e.g., “Order-to-Cash < 24 h”) and review that metric in the CFO’s standing meeting. When a single KPI is visible on the same slide as revenue, executive focus holds.
2 – Legacy Systems Fight Back
Deep-tier batch jobs, undocumented triggers, and brittle flat-file exchanges can derail even a textbook DPA pilot. Impact My Biz
Fix: “strangle-vines” first-expose just the data needed for the pilot behind a thin REST or event façade, then expand coverage flow-by-flow. Our Legacy Modernization Guide outlines this pattern.
3 – Change Resistance at the Front Line
Misalignment between business and technical teams ranks among the top automation blockers for 2024.
Fix: co-design sessions with the people who click the buttons today. Eight hours of workshops beats weeks of re-training later-and surfaces undocumented “Excel glue” before it breaks the pilot.
4 – Security & Compliance Doubts Around Low-Code
Concerns span scalability (32 %), security (25 %), and governance (28 %). OWASP now publishes a Top 10 Low-Code/No-Code Risks to guide enterprise reviews. OWASP Foundation
Fix: treat the DPA platform like any other tier-one system:
- Enforce SSO with MFA and role-based least privilege.
- Automate static scans for every workflow export.
- Record audit trails to your SIEM, not a siloed admin console.
5 – Scope Creep Erodes ROI
Teams see a low-code canvas and want every workflow done “by next sprint.” Delivery velocity drops, stakeholders lose patience.
Fix: cap each release at one KPI and one integration layer. Park everything else in a time-boxed backlog review; most ideas refine themselves or vanish after two weeks.
Proof in Action-Two Enterprise Snapshots
Insurance – Claims Quality Without Extra Headcount
A mid-tier insurer used DPA to orchestrate claims triage, integrating OCR and rules engines to validate submissions in real time. Post-deployment audits showed an 80 % drop in data-entry errors and a 25 % lift in adjuster throughput, freeing underwriters for complex cases while holding staffing flat. Regulatory compliance improved, too: every decision path is now traceable in the workflow log-no more PDF spelunking at audit time.
Manufacturing – Order-to-Cash in Half the Time
A global components maker mapped its fragmented order-to-cash loop: five hand-offs and three overnight batch exports before an invoice could post. By standing up a low-code DPA flow on top of SAP and Salesforce, the team collapsed those hops into a single event-driven sequence. Cycle time fell 42 % within twelve weeks, and finance reported a seven-day cash-flow pull-forward worth ≈ $3 million per quarter. The company now funds each new automation sprint from savings already banked.
Both programmes shared three success factors we highlight throughout this guide:
- Tight KPI ownership (cycle time, error rate) tied to executive OKRs.
- Small, time-boxed pilots that paid for expansion from their own savings.
- Fusion teams-process owners plus citizen devs-who iterate without waiting for central IT.
Proof in Action-Two Enterprise Snapshots
Digital Process Automation turns strategy into repeatable, measurable routines. By:
- Prioritising flows with the biggest cycle-time drag,
- Proving value through a low-risk, low-code pilot, and
- Instrumenting KPIs so sponsors see results weekly,
enterprises create a repayment engine that funds the next wave of automation-and the one after that.
Ready to close your own execution gap? Book a 30-minute scoping call with a DevPulse solutions architect and walk away with a pilot backlog, ROI model, and timeline-no obligation.
Or, dive deeper:
- Custom Software Development for bespoke integrations that extend your DPA reach.
- Tech Consulting Services when legacy blockers stall momentum.
Your strategy is already sound. Let’s make the mechanics unstoppable.